Designing of aseptic area
Designing an aseptic area is crucial for industries like pharmaceuticals, biotechnology, and food processing, where maintaining a sterile environment is essential to prevent contamination of products. Here is a detailed note on designing an aseptic area:
Facility Location and Layout
Choose a location away from sources of contamination such as dust, industrial pollutants, or high traffic areas.
Implement a unidirectional flow of materials and personnel to minimize the risk of cross-contamination.
Design a layout that allows for easy cleaning and maintenance, with clear separation between different process areas.
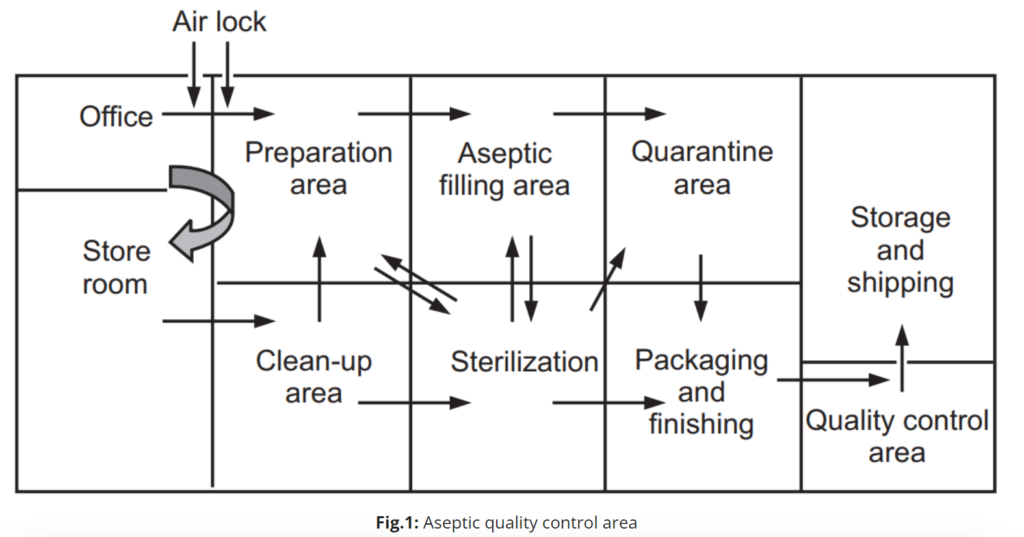
Environmental Controls
Maintain strict control over temperature, humidity, and air pressure within the aseptic area to prevent the growth of microorganisms.
Use HEPA (High-Efficiency Particulate Air) filters to remove particles from the air.
Install airlocks and gowning rooms to control the entry of personnel and materials into the aseptic area.
Cleanroom Classification
Classify the cleanroom based on the level of cleanliness required. Common classifications include ISO 5 (Class 100), ISO 7 (Class 10,000), and ISO 8 (Class 100,000).
Design airflow patterns, such as laminar flow, to maintain cleanliness levels.
Material Selection
Choose materials that are easy to clean and resistant to corrosion and microbial growth.
Use smooth and non-porous surfaces to prevent the accumulation of contaminants.
HVAC System
Implement a robust Heating, Ventilation, and Air Conditioning (HVAC) system with appropriate filtration to maintain clean air.
Regularly monitor and validate the performance of the HVAC system.
Sterilization Methods
Integrate validated sterilization methods for equipment, surfaces, and materials entering the aseptic area.
Common sterilization methods include autoclaving, gamma irradiation, and chemical sterilization.
Gowning Procedures
Establish strict gowning procedures for personnel entering the aseptic area, including the use of sterile garments, gloves, and head coverings.
Provide training on proper gowning techniques to minimize the risk of contamination.
Monitoring and Validation
Implement a comprehensive environmental monitoring program to regularly assess the cleanliness of the aseptic area.
Conduct validation studies to ensure that the design and operational parameters are consistently met.
Emergency Response Plan
Develop a detailed emergency response plan to address any deviations from the aseptic process, including contamination events.
Train personnel on emergency procedures and conduct regular drills.
Documentation and Record Keeping
Maintain detailed documentation of the aseptic area design, construction, and validation processes.
Keep records of environmental monitoring, equipment maintenance, and personnel training.
Regulatory Compliance
Ensure that the design and operation of the aseptic area comply with relevant regulatory guidelines and standards.
Stay informed about updates in regulations and adjust the facility accordingly.
Continuous Improvement
Establish a culture of continuous improvement to adapt to evolving industry standards and technologies.
Conduct regular reviews and audits to identify areas for enhancement.
A well-designed aseptic area is essential for ensuring the quality and safety of products in industries where contamination can have significant consequences. Regular maintenance, monitoring, and adherence to best practices are key elements in the successful operation of such facilities.