\Pharmaceutical Plant Construction
Pharmaceutical plant construction is a highly specialized and intricate process that requires meticulous planning and careful selection of materials to ensure compliance with regulatory standards, durability, efficiency, and cost-effectiveness. The materials used in pharmaceutical plant construction must meet stringent quality and safety requirements to prevent contamination, withstand exposure to aggressive cleaning agents, and maintain structural integrity over extended periods. This selection process is influenced by several factors that determine the overall functionality, efficiency, and safety of the plant.
In pharmaceutical manufacturing, ensuring a sterile and contamination-free environment is of utmost importance. Therefore, the materials used in the construction of cleanrooms, production areas, and storage facilities must be chosen with precision to avoid any risks of cross-contamination or degradation of pharmaceutical products. Additionally, compliance with global regulatory bodies such as the FDA (Food and Drug Administration), EMA (European Medicines Agency), and WHO (World Health Organization) dictates the type of materials that can be used within these facilities. Non-compliance with these regulations can lead to severe consequences such as legal penalties, suspension of production, or even permanent closure of the facility.
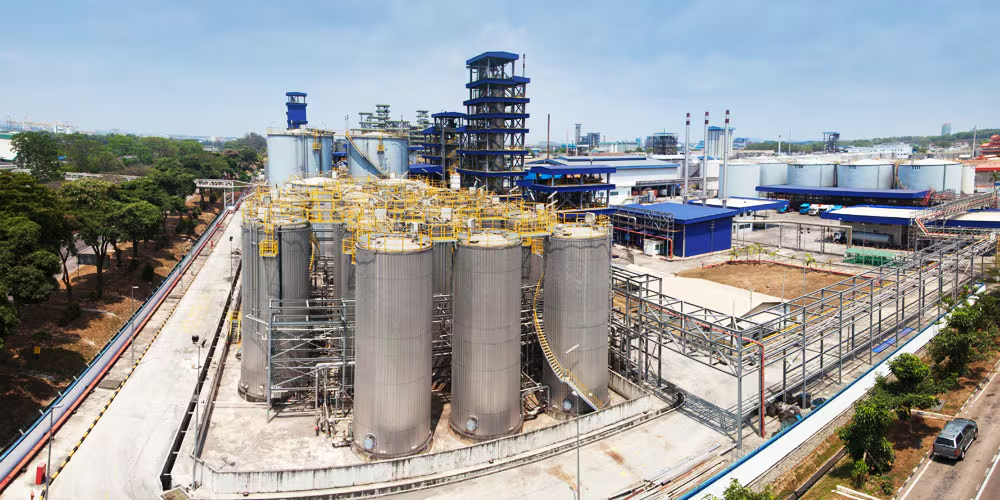
This article explores in detail the various critical factors that influence material selection in pharmaceutical plant construction, providing insights into how each element plays a crucial role in maintaining a safe, hygienic, and efficient manufacturing environment.
1. Regulatory Compliance and Standards
Pharmaceutical plants must comply with stringent regulatory requirements set by various international and national agencies to ensure the safety and efficacy of drug production. These regulatory agencies include:
- FDA (Food and Drug Administration, USA) – Oversees the safety, manufacturing practices, and quality of pharmaceutical products, including the materials used in production facilities.
- EMA (European Medicines Agency) – Regulates pharmaceutical production in the European Union, ensuring that facilities comply with safety, hygiene, and operational protocols.
- WHO (World Health Organization) – Provides international guidelines for pharmaceutical manufacturing, including Good Manufacturing Practices (GMP) standards that emphasize material quality.
- ISO (International Organization for Standardization) – Sets global standards for quality management, such as ISO 14644 for cleanrooms and controlled environments.
- GMP (Good Manufacturing Practices) – A fundamental set of principles ensuring that pharmaceutical products are consistently produced and controlled according to strict quality standards.
Materials should be selected based on their compliance with these regulations to ensure that the facility meets international safety and quality standards. Any deviation from these regulations can lead to non-compliance, resulting in regulatory penalties, production delays, or even plant shutdowns. Moreover, adherence to these standards ensures that the pharmaceutical products manufactured within the facility are free from contamination and meet the highest standards of safety and efficacy.
2. Chemical Resistance
Pharmaceutical plants handle a wide range of chemicals, including solvents, acids, alkalis, and disinfectants. As a result, materials must be chosen based on their ability to withstand chemical exposure without degrading, corroding, or contaminating pharmaceutical products. Some key considerations include:
- Corrosion and Oxidation Resistance – Stainless steel, particularly SS 316L, is widely used in pharmaceutical facilities due to its superior corrosion resistance compared to SS 304. It prevents rust formation and contamination, making it ideal for processing equipment, piping systems, and storage tanks.
- Resistance to Harsh Cleaning Agents – Many cleaning and sanitization procedures involve strong disinfectants and sterilizing agents, such as hydrogen peroxide, sodium hypochlorite, and ethanol. Materials like PTFE (Polytetrafluoroethylene), PVDF (Polyvinylidene fluoride), and high-grade polymers are selected for their chemical stability.
- Non-reactive Nature – Materials used in contact with pharmaceutical products must not react with chemicals, ensuring product purity and preventing undesired chemical interactions. Glass and high-quality plastics are commonly used for this reason.
The ability of materials to resist chemical damage contributes to the overall longevity of the facility, reducing the need for frequent maintenance and replacements, which can be both costly and time-consuming.
3. Contamination Control
Contamination control is one of the most critical aspects of pharmaceutical manufacturing. The materials selected for plant construction must minimize the risk of microbial growth, particle shedding, and cross-contamination. The ideal materials should possess the following properties:
- Non-porous Surface – Materials should be smooth and non-porous to prevent bacterial adhesion and microbial growth. Stainless steel, glass, and coated surfaces such as epoxy resins are widely used for this reason.
- Easy-to-clean and Sterilizable – Materials must allow for frequent cleaning with minimal effort while maintaining structural integrity. Materials that support steam sterilization, autoclaving, and chemical disinfection are preferred in cleanroom environments.
- Resistance to Biofilm Formation – Certain materials, such as uncoated plastics, can harbor bacteria and biofilms, posing a risk to product integrity. Using antimicrobial coatings and selecting appropriate materials mitigates this risk.
Strict adherence to contamination control measures ensures that pharmaceutical products remain free from impurities, thereby enhancing their safety, stability, and efficacy for consumers.
4. Mechanical Strength and Durability
Materials used in pharmaceutical plants must possess excellent mechanical strength to withstand operational stress, temperature variations, and prolonged use without degradation. Factors to consider include:
- Load-bearing Capacity – Structural materials such as reinforced concrete and stainless steel must support heavy equipment, maintain stability, and ensure long-term durability.
- Impact Resistance – Equipment and facility components should be able to endure mechanical shocks without deforming or breaking. Polycarbonate and high-strength alloys are often used in impact-prone areas.
- Temperature Tolerance – Many pharmaceutical processes involve extreme temperatures, from deep freezing to high-temperature sterilization. Materials should retain their mechanical properties across these temperature variations.
The use of high-quality, durable materials ultimately reduces long-term maintenance costs, enhances safety, and ensures the longevity of the facility.
5. Cost-effectiveness
The economic aspect of material selection cannot be ignored. Pharmaceutical companies must balance material quality, compliance, and durability with cost constraints. Considerations include:
- Initial Investment vs. Long-term Costs – High-quality materials such as SS 316L have higher upfront costs but lower maintenance costs due to their superior corrosion resistance.
- Availability and Supply Chain Factors – Readily available materials minimize lead times, reduce procurement costs, and prevent delays in construction.
- Operational Efficiency – Materials that enhance productivity and minimize downtime contribute to long-term cost savings.
A strategic approach to material selection can help companies achieve cost-effectiveness without compromising on quality and regulatory compliance.
6. Environmental Sustainability
Sustainability has become a major focus in pharmaceutical plant construction. Companies are increasingly opting for eco-friendly materials that reduce environmental impact. Key considerations include:
- Recyclable and Sustainable Materials – Stainless steel and aluminum can be recycled, contributing to sustainability efforts.
- Energy-efficient Materials – Insulation materials that reduce energy consumption in HVAC systems improve overall sustainability.
- Low Environmental Impact Production – Sustainable sourcing of materials minimizes ecological damage and promotes green construction practices.
Using sustainable materials helps companies align with global environmental regulations while reducing operational costs and promoting corporate social responsibility.
Conclusion
Material selection for pharmaceutical plant construction is a multifaceted process that involves careful consideration of regulatory compliance, chemical resistance, contamination control, durability, cost-effectiveness, thermal properties, sustainability, and safety. The right choice of materials ensures a safe, efficient, and compliant manufacturing environment, ultimately contributing to product quality and operational efficiency.
By integrating the right materials into plant design and construction, pharmaceutical manufacturers can create state-of-the-art facilities that meet industry standards, enhance productivity, and ensure the highest levels of safety and hygiene in drug manufacturing processes. A well-structured approach to material selection can lead to cost savings, improved manufacturing efficiency, and regulatory approval, making it a crucial aspect of pharmaceutical plant design and operation.