Principles:
A ball mill is a type of grinder or mill used to mill the materials into fine powder in pharmaceutical, chemical, or metallurgical industries. Ball milling relies on the impact and attrition between the balls impacting the material to be ground and the grinding media.
Construction:
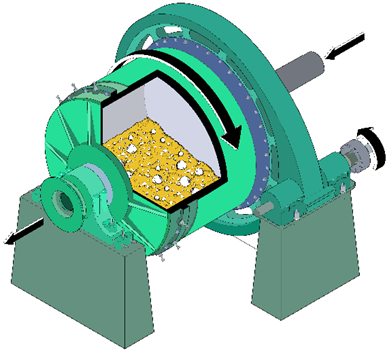
1. Cylindrical Shell: The ball mill consists of a hollow cylindrical shell that rotates about its axis. The shell is usually made of steel, stainless steel, or rubber.
2. Liners: An abrasion-resistant material such as manganese steel or rubber typically lines the inner surface of the cylindrical shell to protect it from wear due to the grinding action.
3. Balls: They place steel or ceramic balls, typically used as grinding media in a ball mill, inside the shell and rotate them with it.
4. Feed and Discharge: Entering the hollow shell at the top, the material to be ground exits through the bottom of the shell after the grinding process.
5. Drive System: A motor rotates the shell through a gearbox, inducing the grinding media and the material to be ground to tumble.
Working:
1. Loading and Rotation: Loading the material to be ground into the cylindrical shell, the mill is then rotated at a critical speed, where the centrifugal force equals the gravitational force acting on the grinding media.
2. Impact and Attrition: As the mill rotates, the grinding media (balls) collide with the material, crushing and grinding it. This impact and attrition process reduce the size of the material.
3. Reduction to Fine Powder: The grinding continues until the material is reduced to a fine powder. The finer the powder, the smaller the particle size achieved.
4. Control of Particle Size: Varying the size and quantity of the grinding media, adjusting the speed of the mill, and controlling the duration of the milling process actively determine the final particle size.
Uses:
1. Grinding and Pulverization:Various industries, including mining, cement, pharmaceuticals, and ceramics, widely use ball mills for grinding and pulverizing materials.
2. Material Mixing: Industries, such as chemical engineering, use them for mixing and blending various materials.
3. Particle Size Reduction: Ball mills are effective in reducing the particle size of materials, making them suitable for a range of applications.
Merits:
1. Versatility: Suitable for both dry and wet grinding operations, allowing for a wide range of applications.
2. Efficiency: The grinding media generates high grinding efficiency through the impact and attrition forces.
3. Controllable Particle Size: Adjusting various parameters actively controls the final particle size, offering flexibility in product specifications.
4. Scale-Up Capability: Suitable for both laboratory-scale and industrial-scale operations, allowing for easy scale-up.
Demerits:
1. High Energy Consumption: Ball mills often require high energy input for the grinding process, making them less energy-efficient compared to some other milling techniques.
2. Wear and Tear: The grinding media and liners experience wear, requiring regular maintenance and replacement.
3. Contamination: There is a possibility of contamination from the grinding media or the lining material, which may affect the purity of the final product in certain applications.
4. Noise and Vibration: The rotating action of the mill can generate noise and vibration, which may require additional measures for noise control and equipment stability.
Ball mills are versatile and widely used for various grinding and milling applications. Understanding their principles, construction, working, uses, merits, and demerits is crucial for optimizing their performance in different industrial processes.