Introduction
Distillation under reduced pressure, often referred to as vacuum distillation, is a process that involves the distillation of liquids at pressures lower than atmospheric pressure. This method is particularly useful for separating components with high boiling points or those prone to thermal degradation at elevated temperatures. The basic principles and methodology of distillation under reduced pressure play a crucial role in achieving efficient separation while minimizing thermal stress on the components.
Basic Principles of Distillation under Reduced Pressure
a. Lower Boiling Points:
– Reduced pressure lowers the boiling points of liquids, enabling the separation of components that would otherwise decompose at higher temperatures.
b. Vapor Pressure:
– At reduced pressure, the vapor pressure of a liquid surpasses the pressure in the distillation system, allowing vaporization at lower temperatures.
c. Enhanced Volatility:
– Components with higher boiling points become more volatile under reduced pressure, facilitating their separation.
d. Thermal Stress Reduction:
– Operating at lower temperatures reduces thermal stress on heat-sensitive compounds.
Methodology of Distillation under Reduced Pressure
a. Apparatus:
1. Distillation Flask:
Contains the liquid mixture to be distilled.
2. Vacuum System:
A vacuum pump or system reduces the pressure within the distillation apparatus.
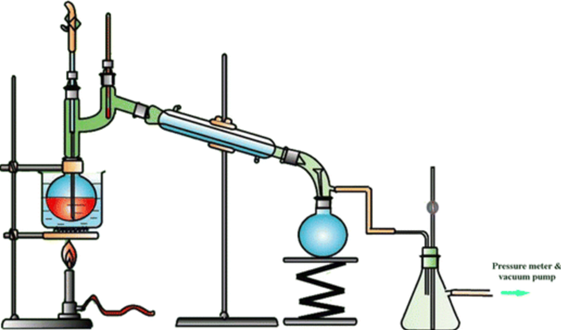
3. Condenser:
Converts vapor back into liquid distillate.
4. Receiver Flask:
Collects the separated components.
5. Heating Source:
Provides heat to the distillation flask.
b. Procedure:
1. Loading the Flask:
The liquid mixture is placed in the distillation flask.
2. Vacuum System Activation:
The vacuum system is activated to reduce the pressure within the apparatus.
3. Heating:
The flask is heated, and the reduced pressure lowers the boiling points of the components.
4. Vaporization:
Vaporization occurs at lower temperatures due to the reduced pressure.
5. Condensation:
The vapor rich in the more volatile component condenses and is collected in the receiver flask.
6. Temperature Monitoring:
Temperature is monitored to prevent excessive heating.
7. Analysis of Fractions:
Fractions collected at different temperature ranges represent different components of the mixture.
c. Factors Influencing Distillation under Reduced Pressure:
1. Vacuum Level:
The level of vacuum determines the degree of pressure reduction and, consequently, the boiling points of the components.
2. Heat Source Control:
Controlling the heat source prevents excessive bumping or boiling over, even at reduced pressures.
3. Condensation Efficiency:
Efficient condensation ensures the collection of pure distillate.
4. Uses:
1. Pharmaceutical Industry:
Commonly used for the separation and purification of heat-sensitive pharmaceutical compounds.
2. Petrochemical Industry:
Applied in the refinement of high-boiling-point hydrocarbons in the petrochemical industry.
3. Food and Beverage Industry:
Used for the extraction and concentration of flavors and fragrances in the food and beverage industry.
4. Chemical Industry:
Distillation under reduced pressure is employed in various chemical processes for separation and purification.
Merits of Distillation under Reduced Pressure
1. Lower Thermal Stress:
Reducing pressure minimizes thermal stress on heat-sensitive compounds.
2. Lower Boiling Points:
Allows for the separation of components with higher boiling points.
3. Improved Separation Efficiency:
Enhanced volatility under reduced pressure leads to improved separation efficiency.
Demerits Distillation under Reduced Pressure
1. Complex Equipment:
Vacuum distillation setups can be more complex and expensive than atmospheric distillation setups.
2. Potential for Contamination:
The reduced pressure may increase the risk of contamination if proper precautions are not taken.
3. Energy Consumption:
Vacuum systems may consume additional energy.
Distillation under reduced pressure is a valuable technique for separating and purifying components that are sensitive to high temperatures. Understanding the basic principles and adhering to proper methodologies are crucial for achieving efficient distillation and obtaining high-purity fractions. This method finds widespread applications in various industries where the separation of heat-sensitive components is essential.