A Double cone blender is a competent and versatile machine used for uniform blending of granules and dry powders.
It is made up of stainless steel.
It is available in various working capacities ranging from 5 – 500 liters.
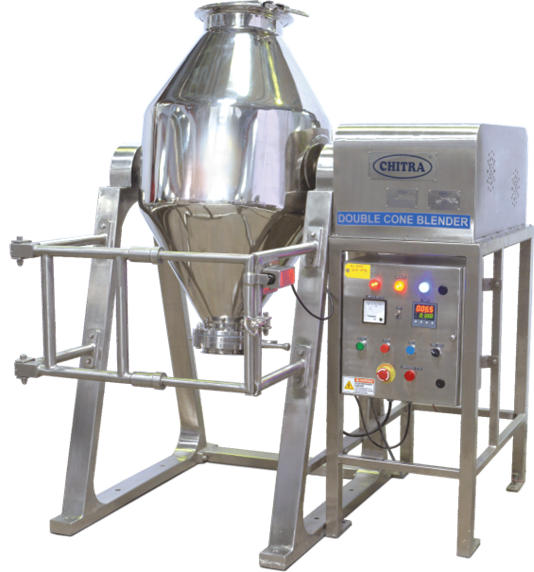
Principle
A double-cone blender produces a homogeneous solid-solid mixture.
This equipment involves axial mixing as the powder moves in different sections.
This blender provides thorough mixing depending on its speed of rotation.
Construction
The body of the double cone blender consists of two cone-shaped sections.
These are joined to a central cylindrical section at their bases.
The rotational axis is perpendicular to the cone axis and passes through the cylindrical section.
Two lateral supports hold the blender body.
One of these supports is fitted with the driving motor.
Working
- With the help of a moving wheel, adjust the angle of the autoclaved double-cone blender so that the material can be conveniently loaded.
- After loading, close the lid of the blender and secure it by fitting the safety pin within its groove.
- Then, the safety guard is put on, and the equipment is switched on.
- After blending, remove the safety guard (only after switching the equipment off), adjust the blender to an angle for convenient unloading of the material, unlock the safety pin, and open the lid.
Applications
This is employed in different industries to prepare pharmaceutical, food, chemical, cosmetic products, etc.
It is used for uniform mixing of granules or dry powders.
It is used to prepare pharmaceuticals, food, and chemical products.
This is suitable for homogeneous mixing of small amounts of powders.
It provides a heating and cooling effect with the help of jacketed construction.
Merits
1) Large quantities of material can be easily handled.
2) It requires minimum maintenance cost.
3) It can be easily cleaned and maintained.
4) It can be easily operated with easy charging and discharging of the material.
Demerits
1. It requires a large headspace for installation
2. insufficient shearing force makes it unsuitable for materials with large differences in particle size distribution or systems containing fine particles.