Principles:
A heavy, flat or muller wheel mounted on a horizontal shaft rotates against a stationary base in the end runner mill, which is a type of edge runner mill. Feeding the material to be ground between the rotating wheel and the stationary base achieves the grinding action through the crushing, grinding, and shearing forces generated by the rotating wheel.
Construction:
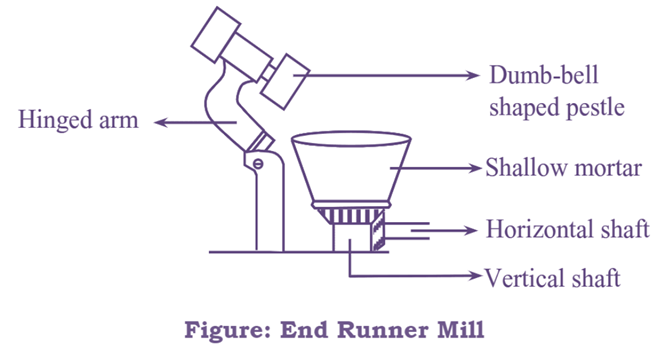
1. Runner Wheel: A heavy, flat or muller wheel mounted on a horizontal shaft. The wheel is often made of hard materials like stone, metal, or wood.
2. Base Plate: A stationary flat surface against which the material is crushed. The base plate provides support for the runner wheel and helps create the grinding action.
3. Horizontal Shaft: A drive mechanism imparts rotational motion to the horizontal shaft connected to the mounted runner wheel.
4. Feed Mechanism: Feeding the material to be ground typically near the center of the mill takes place between the rotating runner wheel and the stationary base plate.
5. Scrapers: To ensure a continuous feed of material into the grinding zone, blades or scrapers are attached to the arms of the runner wheel.
Working:
1. Material Feeding: The material is fed between the rotating runner wheel and the stationary base plate.
2. Crushing, Grinding, and Shearing: The rotating motion of the runner wheel crushes, grinds, and shears the material against the stationary base plate, resulting in size reduction.
3. Continuous Feed: Scrapers or blades attached to the arms of the runner wheel ensure a continuous feed of material into the grinding zone.
4. Discharge: The reduced material exits the mill from the periphery of the grinding zone.
Uses:
1. Grinding and Crushing: The primary use of the end runner mill is for grinding and crushing materials into fine powders.
2. Mixing and Blending: It can be used for mixing and blending purposes, especially in the preparation of wet pastes.
3. Size Reduction of Wet Material: Particularly effective for size reduction of wet materials due to the crushing and shearing action.
Merits:
1. Simple Design: The end runner mill has a simple and robust design, making it easy to operate and maintain.
2. Versatility: Suitable for a wide range of materials, including those that are wet, sticky, or contain moisture.
3. High Crushing Efficiency: The crushing, grinding, and shearing action of the rotating wheel allows for effective size reduction.
4. Cost-Effective: Compared to some other grinding mills, the end runner mill is often considered cost-effective.
Demerits:
1. Low Energy Efficiency: End runner mills may have lower energy efficiency compared to some modern grinding mills.
2. Limited Control over Particle Size: Achieving precise control over particle size distribution can be challenging with end runner mills.
3. Wear and Tear: The contact between the runner wheel and the base plate can lead to wear and tear, requiring maintenance and replacement of parts.
4. Limited Scale: May not be suitable for large-scale industrial applications due to limitations in throughput and efficiency.
The end runner mill is a traditional grinding mill that has found applications in various industries. Understanding its principles, construction, working, uses, as well as merits and demerits is essential for assessing its suitability in different processes.