The filter leaf, also known as the leaf filter, is a type of pressure filter used in industrial processes for the separation of solids from liquids. It is commonly utilized in applications requiring efficient, continuous filtration, such as in the pharmaceutical, food, beverage, chemical, and petroleum industries.
1. Definition
A filter leaf is a filtration system that uses multiple perforated metal plates, covered with filter cloth or mesh, mounted within a pressure vessel. Each metal plate or “leaf” acts as an individual filter unit that separates solid particles from a liquid, which is driven by pressure through the filter medium.
2. Principle
The filter leaf operates on the principle of pressure filtration. The liquid to be filtered (the feed) is forced through the filter media covering each leaf by applying pressure within the closed vessel. The filter cloth or mesh retains the solid particles, forming a filter cake on the surface, while the filtrate passes through the filter medium and is collected on the opposite side.
3. Construction
The filter leaf consists of the following main components:
Filter Leaves: Each leaf is made up of a perforated metal plate, often in a rectangular or circular shape, covered with a filter cloth or mesh. The leaf allows for the formation of a filter cake on its surface.
Filter Cloth or Mesh: This acts as the filter media, allowing only the liquid to pass through while retaining solids.
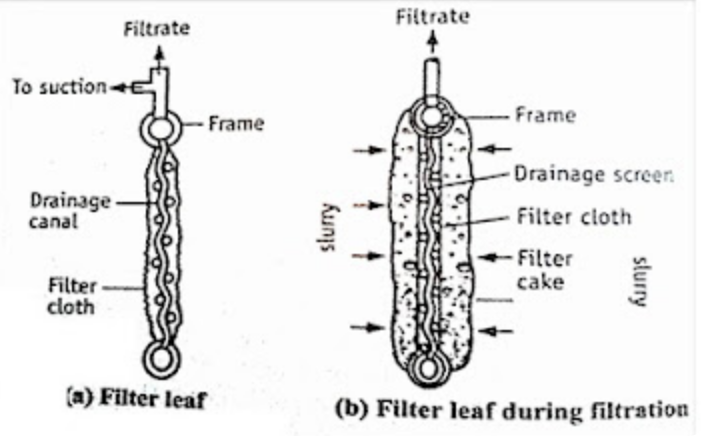
Manifold and Filtrate Outlet: The filtrate from each leaf is collected through a central manifold or filtrate channel, which directs the liquid out of the pressure vessel.
Pressure Vessel: The vessel holds the filter leaves and creates a sealed chamber where pressure can be applied for filtration.
Agitation System (optional): Some filter leaf systems have an agitator to keep solids in suspension, improving filtration efficiency.
4. Working
The working of a filter leaf system follows these steps:
1. Feed Introduction: The unfiltered liquid or slurry is pumped into the pressure vessel containing multiple filter leaves, each with its own filter media.
2. Filtration Process: As the pressure increases within the vessel, the liquid is forced through the filter cloth, which retains the solid particles, forming a cake on the surface of each leaf. The filtered liquid passes through the perforations in the leaf, flowing into the central manifold.
3. Filtrate Collection: The filtrate flows out of each leaf into the manifold, where it is collected and directed out of the vessel through the outlet.
4. Filter Cake Removal: After filtration, the filter cake is either manually or automatically removed. In some systems, air or gas is used to backflush the leaves, detaching the filter cake from the surface.
5. Cleaning and Reassembly: The filter leaves and cloths are cleaned, reassembled, and prepared for the next filtration cycle.
5. Uses
The filter leaf system is versatile and widely used in various industries, including:
Pharmaceutical Industry: For purifying liquids, extracting active ingredients, and clarifying injectable drugs.
Chemical Industry: Used for separating chemical intermediates and removing impurities from solvents and solutions.
Food and Beverage Industry: Common in edible oil refining, juice clarification, and sugar syrup filtration.
Petroleum Industry: For filtration of lubricating oils, fuel, and other petrochemical products.
Wastewater Treatment: Effective in removing suspended solids from wastewater in industrial processes.
6. Merits
The filter leaf system offers several advantages:
High Filtration Efficiency: Capable of removing even small particles, providing high-purity filtrate.
Large Filtration Area: Due to the multiple leaves, it offers a large surface area for filtration within a compact setup.
Minimal Floor Space Requirement: Since the leaves are stacked vertically in a pressure vessel, it requires less space.
Continuous Operation: Allows for batch processing, enabling continuous filtration without frequent downtime.
Easy Filter Cake Removal: Backflushing allows for easy cake detachment, simplifying cake removal.
Low Maintenance: Simple design reduces maintenance requirements compared to other filter types.
7. Demerits
Despite its benefits, the filter leaf system has limitations:
High Initial Setup Cost: The pressure vessel and multiple leaves can make it a costly investment.
Clogging of Filter Cloth: Fine particles and viscous liquids can cause clogging, necessitating frequent cleaning.
Requires Skilled Operation: Efficient operation and maintenance of the system require trained personnel.
Not Ideal for High Solid Content: Leaf filters are better suited for low to medium solid concentrations, as high solids may lead to frequent clogging.
Limited in Highly Corrosive Applications: The metal components are vulnerable to certain highly corrosive chemicals, which may require special materials.
Summary Table
Aspect | Filter Leaf |
Definition | A filtration system that uses perforated metal plates covered with filter cloth, arranged within a pressure vessel for solid-liquid separation. |
Principle | Pressure filtration through filter media on each leaf, with solids retained as filter cake and liquid passing through as filtrate. |
Construction | Filter leaves (metal plates with cloth), pressure vessel, manifold, and optional agitator system. |
Working | Feed introduction, filtration through leaves, filtrate collection, filter cake removal, and cleaning. |
Uses | Pharmaceutical purification, chemical separation, food/beverage clarification, oil filtration, and wastewater treatment. |
Merits | High filtration efficiency, compact design, minimal floor space, continuous operation, easy cake removal, and low maintenance. |
Demerits | High setup cost, clogging potential, requires skilled operation, less effective for high solid content, and limited suitability for highly corrosive applications. |
Conclusion
The filter leaf system is a robust and efficient filtration method, ideal for industries requiring consistent high-quality filtration. While it has specific limitations, its compact design, high efficiency, and adaptability make it a valuable choice for many industrial applications. Understanding its design, operating principles, and maintenance requirements can significantly enhance its effectiveness in various filtration processes.