The pharmaceutical industry uses a specialized mechanical device called a pharmaceutical hammer mill to reduce the particle size of pharmaceutical materials, including active pharmaceutical ingredients (APIs), excipients, and other powders. It works by subjecting these materials to a series of hammers or blades that impact and grind them into smaller, more manageable particles. Pharmaceutical hammer mills meet strict regulatory and quality standards, ensuring they maintain the consistency and quality of pharmaceutical products used in various dosage forms like tablets, capsules, and powders.
Objectives/Applications in Pharmaceuticals
The use of hammer mills in the pharmaceutical industry serves several important objectives and applications, including:
1. Size Reduction: Hammer mills are primarily employed to reduce the particle size of pharmaceutical materials. This is crucial in pharmaceutical manufacturing, as it helps ensure consistent product quality and performance.
2. Granulation: You can use hammer mills for wet or dry granulation processes, where they agglomerate pharmaceutical powders into controlled-size granules. Granulation is a common step in tablet and capsule manufacturing.
3. Crushing and Pulverization: Some pharmaceutical materials must be crushed or pulverized to create fine powders. Hammer mills are suitable for achieving this, ensuring uniform particle size for further processing.
4. Milling Active Ingredients: To improve the solubility, bioavailability, and overall performance in drug formulations, pharmaceutical manufacturers often mill or micronize active pharmaceutical ingredients (APIs). They can achieve this purpose by using hammer mills.
5. Deagglomeration: Pharmaceutical materials may become agglomerated during storage or transportation. Hammer mills can effectively deagglomerate these materials, ensuring they are suitable for further processing.
Principles of Hammer mill
The principle of a hammer mill in pharmaceuticals, as in other industries, is based on the fundamental concept of size reduction through high-speed impact and controlled particle size.
Material Size Reduction
The primary objective of a pharmaceutical hammer mill is to reduce the size of pharmaceutical materials. This is crucial in the pharmaceutical industry, as it ensures that the ingredients used in drug formulations are of a consistent and controlled particle size. The following steps accomplish size reduction:
a. Material Feeding: Pharmaceutical materials, such as active pharmaceutical ingredients (APIs), excipients, or drug intermediates, are fed into the hammer mill through the feed inlet.
b. Rotor Rotation: Inside the hammer mill, there is a rotor equipped with hammers. The rotor rapidly rotates, generating centrifugal force and causing the hammers to move outward from the center.
c. High-Speed Impact: The rapidly moving hammers subject the materials to high-speed impact forces as they come into contact with them. The impact between the hammers and the material shatters and reduces the material into smaller particles.
d. Controlled Particle Size: Several factors, including the size and speed of the hammers and the perforation size of the screen located at the bottom of the grinding chamber, determine the size of the final product.Adjusting these parameters allows for precise control over the particle size.
Size Consistency
In pharmaceutical manufacturing, it is essential to achieve a consistent and controlled particle size for the raw materials used in drug formulations. This consistency ensures that the drug products have uniform quality and performance. The hammer mill provides a reliable method for achieving the desired particle size, critical for product efficacy and manufacturing efficiency.
Milling and Micronization
Pharmaceutical hammer mills not only reduce size but also mill and micronize active pharmaceutical ingredients (APIs). This process is crucial to improve the solubility and bioavailability of poorly water-soluble drugs. The hammer mill helps reduce the API particle size to a range that is more suitable for drug formulation, ensuring the drug’s therapeutic effectiveness.
Construction of Hammer mill
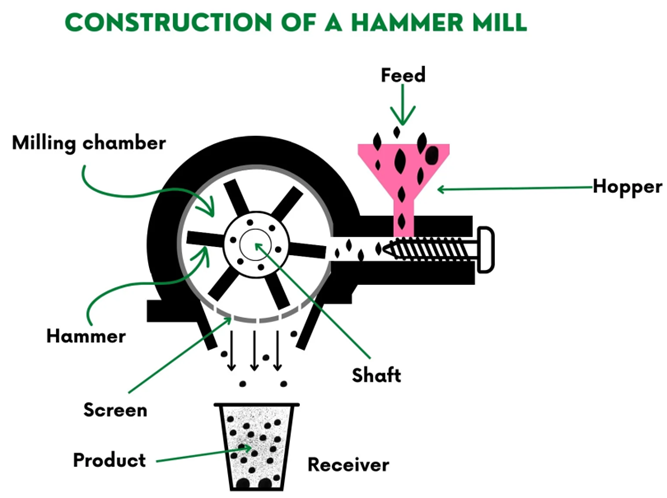
The construction of a pharmaceutical hammer mill is designed to meet specific industry requirements, with a focus on safety, hygiene, and precision for pharmaceutical processing. Here’s a detailed note on the construction of a pharmaceutical hammer mill:
1. Stainless Steel Construction
In pharmaceutical applications, the construction material of the hammer mill is often stainless steel. This choice is primarily for its resistance to corrosion, ease of cleaning, and compliance with stringent hygiene and regulatory standards.
2. Enclosed Design
Pharmaceutical hammer mills typically feature an enclosed design to prevent dust and product contamination. The enclosure may include transparent or removable panels for inspection and maintenance purposes.
3. Grinding Chamber
The grinding chamber is where the actual size reduction takes place. It houses the rotor and hammers, and it may include wear-resistant liners to prolong the equipment’s lifespan. The chamber is designed to be easy to clean and sanitize to meet pharmaceutical industry standards.
4. Rotor
The rotor is a rotating shaft that holds the hammers. It is a critical component responsible for the high-speed impact that reduces the material size. Typically, manufacturers construct the rotor from stainless steel and precisely balance it to minimize vibration and ensure stable operation.
5. Hammers
The hammers are the striking elements of the hammer mill. In pharmaceutical applications, manufacturers often make them from stainless steel or other materials compatible with pharmaceutical processes. These hammers can be swinging or fixed, depending on the specific requirements of the process.
6. Screen
The bottom of the grinding chamber features a screen with perforations. The size of the perforations determines the particle size of the final product. Manufacturers also construct screens from stainless steel and design them for easy removal and replacement to adjust the screen size.
7. Feed Inlet
Pharmaceutical materials enter the hammer mill through a feed inlet. This inlet is designed to facilitate material flow and minimize the risk of contamination.
8. Discharge Outlet
Processed pharmaceutical materials exit the mill through a discharge outlet. The design of the outlet allows for efficient product removal and permits positioning to collect the milled material in a container or convey it further in the production process.
9. Drive System
A drive motor powers the rotor’s rotation and the operation of the hammer mill.Designers of pharmaceutical hammer mills incorporate precision and control into the drive system, allowing for the adjustment of rotor speed to achieve the desired particle size.
10. Control and Monitoring Systems
Many pharmaceutical hammer mills have control systems that allow operators to set and monitor various parameters, including rotor speed, feed rate, and screen perforation size. These systems enhance the precision of the size reduction process.
11. Safety Features
Safety is a paramount concern in pharmaceutical construction. The equipment often includes safety interlocks and guards to prevent accidental access to moving parts and ensure operator protection.
12. Compliance with Regulations
Pharmaceutical hammer mills are designed to meet pharmaceutical regulations and standards, including cGMP (current Good Manufacturing Practices) and FDA guidelines. Manufacturers must ensure that their equipment is compliant with these requirements, which may include the use of appropriate materials, finishes, and documentation.
The construction of a pharmaceutical hammer mill tailors it to the specific needs of the pharmaceutical industry, ensuring product safety, hygiene, and precision in size reduction processes.These design considerations make pharmaceutical hammer mills suitable for various applications, including milling, micronizing, and granulating pharmaceutical materials.
Working of Hammer mill
The working of a pharmaceutical hammer mill is based on the fundamental principles of size reduction through high-speed impact and controlled particle size. Here’s a detailed explanation of how a pharmaceutical hammer mill operates:
1. Material Feeding
The pharmaceutical material to be processed is introduced into the hammer mill through the feed inlet. This can be a manual or automated process, depending on the specific equipment and application.
2. Rotor Rotation
Inside the hammer mill, there is a rotor, typically made of stainless steel, with hammers attached to it. The rotor rapidly rotates, creating a centrifugal force that propels the hammers outward from the center. The rotor’s speed is controlled to achieve the desired particle size reduction.
3. High-Speed Impact
As the pharmaceutical material enters the grinding chamber, it comes into contact with the rapidly moving hammers. These hammers deliver high-speed impacts to the material, resulting in the shattering and reduction of the material into smaller particles.
4. Controlled Particle Size
The size of the final product is controlled and determined by several factors:
– Hammer Size and Configuration: The size and configuration of the hammers, as well as their impact force, play a critical role in determining the extent of size reduction.
– Rotor Speed: The rotor’s speed affects the intensity of the impact. Adjusting the rotor speed allows for control over the degree of size reduction.
– Screen Perforation Size: At the bottom of the grinding chamber, there is a screen with perforations of a specific size. This screen acts as a sieve, allowing only particles smaller than the perforation size to pass through. Adjusting the perforation size of the screen controls the final particle size.
5. Particle Separation
Smaller particles, reduced to the desired size, pass through the screen and exit through the discharge outlet of the hammer mill. In pharmaceutical manufacturing, this material can be collected in a container or conveyed further.
6. Quality Control
Operators can monitor and control various parameters during the operation, such as rotor speed, feed rate, and screen perforation size, to ensure that the final product meets the specifications for particle size and quality.
7. Continuous or Batch Operation
Pharmaceutical hammer mills can operate in either a continuous or batch mode, depending on the specific processing requirements and equipment design. Continuous operation is suitable for large-scale production, while batch operation is used for smaller quantities or when frequent adjustments are needed.
8. Cleaning and Maintenance
After processing, the equipment must be cleaned and sanitized to prevent cross-contamination of pharmaceutical materials. The design of pharmaceutical hammer mills often includes features that facilitate easy cleaning and maintenance, such as removable panels and access points.
The working of a pharmaceutical hammer mill is based on the principles of high-speed impact and controlled particle size reduction. By adjusting parameters such as hammer size, rotor speed, and screen perforation size, operators can precisely control the final particle size of pharmaceutical materials, ensuring consistency and quality in pharmaceutical manufacturing processes. Pharmaceutical hammer mills are constructed and designed to meet strict industry regulations and hygiene standards, making them suitable for producing pharmaceutical products.