A propeller in the pharmaceutical context is a mechanical device used for mixing liquids in tanks or vessels. It consists of blades that rotate around a central shaft, creating fluid motion and ensuring homogenous mixing of pharmaceutical solutions, suspensions, or emulsions.
Principles of Mixing with Propellers
1. Fluid Dynamics: The fundamental principle governing propeller mixing is fluid dynamics, which involves the study of forces and motion in fluids. When the propeller blades rotate, they impart energy to the liquid, causing it to flow and mix.
2. Shear and Turbulence: The design of the propeller blades determines the type of flow generated. High shear mixing occurs when the propeller creates a turbulent flow, promoting efficient mixing by reducing particle size and enhancing the dispersion of ingredients.
3. Centrifugal Force: As the propeller blades spin, they create centrifugal force that pushes the liquid outward, resulting in circulation patterns that facilitate mixing.
4. Volume and Flow Rate: The volume of the liquid being mixed and the speed of the propeller affect the mixing efficiency. Larger volumes may require more powerful propellers to achieve the desired mixing.
Construction
1. Shaft: The central component that connects the propeller to the motor. It transmits the rotational force.
2. Blades: The crucial part of the propeller, typically made from stainless steel or other corrosion-resistant materials, designed to optimize flow patterns. Blade shapes can vary (e.g., flat, pitched) depending on the intended mixing application.
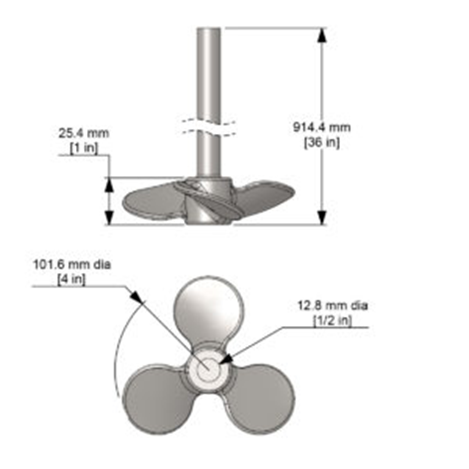
3. Motor: Provides the necessary rotational force for the propeller. The motor’s power and speed settings can often be adjusted based on the mixing requirements.
4. Mounting Frame: Supports the propeller assembly and motor, ensuring stability during operation.
5. Variable Speed Drive (Optional): Allows for control over the propeller’s speed, providing flexibility for different mixing tasks.
Working
1. Installation: The propeller is mounted inside a mixing vessel filled with the liquid to be mixed. It is submerged to a specified depth to optimize mixing.
2. Powering the Motor: Once the system is set up, the motor is powered on, causing the shaft to rotate.
3. Fluid Motion: As the blades turn, they create a flow of liquid, drawing material from the bottom and pushing it upwards, while also pulling material from the sides towards the center. This action promotes mixing.
4. Monitoring and Control: Parameters like mixing speed, duration, and temperature are monitored throughout the process to ensure optimal conditions are maintained.
Uses
1. Homogenization: Ensuring uniform distribution of active pharmaceutical ingredients (APIs) in suspensions and emulsions.
2. Dissolution: Aiding in dissolving solid substances into liquids, critical for the formulation of solutions.
3. Blending: Mixing powders or granules with liquids for uniform consistency in preparations.
4. Emulsification: Creating stable emulsions from immiscible liquids, such as oil and water, commonly used in topical and injectable formulations.
5. Heat Transfer: Facilitating heat transfer during processes like sterilization or temperature-sensitive formulations.
Merits
1. Efficiency: High mixing efficiency can be achieved in a relatively short time, ensuring quick processing.
2. Scalability: Suitable for both small-scale laboratory applications and large-scale production in pharmaceutical manufacturing.
3. Versatility: Can be used with a variety of liquid formulations, including viscous and non-viscous liquids.
4. Cost-Effectiveness: Low operational costs and maintenance, especially in continuous mixing processes.
5. Customization: Propellers can be designed and adjusted for specific mixing tasks based on the formulation and desired outcome.
Demerits
1. Energy Consumption: High power requirements, especially for large vessels or high viscosity fluids, can lead to increased operational costs.
2. Wear and Tear: Continuous operation can lead to wear on the propeller blades, necessitating periodic replacement.
3. Poor Mixing in Dead Zones: In some configurations, propellers may create dead zones where mixing is inadequate, leading to inconsistencies.
4. Heat Generation: Excessive mixing can generate heat, which might be detrimental to heat-sensitive formulations.
5. Not Suitable for All Formulations: Some delicate formulations may require gentler mixing methods to prevent degradation or damage to active ingredients.
Conclusion
Propellers are essential tools in the pharmaceutical industry for achieving efficient mixing of various liquid formulations. Their design and operational parameters must be carefully considered to optimize performance while minimizing drawbacks. Proper understanding and application of propellers can significantly enhance the quality and consistency of pharmaceutical products.