A rotary drum filter is a type of vacuum filter widely used for continuous separation of liquids from solids in various industrial processes. The filter is particularly efficient for handling large volumes of slurry and is popular in industries such as pharmaceuticals, chemicals, food and beverages, wastewater treatment, and mining.
1. Definition
A rotary drum filter is a continuous filtration device with a cylindrical drum that rotates around its horizontal axis, partially submerged in a slurry tank. As the drum rotates, a vacuum is applied to the inner surface, drawing liquid through a filter cloth while retaining solids on the surface, forming a filter cake. The cake is subsequently dried, washed, and discharged.
2. Principle of Rotary Drum Filter
The rotary drum filter operates on the principle of vacuum filtration. A vacuum is applied inside the drum, which creates a pressure differential across the filter media covering the drum surface. This pressure differential forces the liquid from the slurry to flow through the filter media, leaving the solid particles as a filter cake on the drum’s outer surface. The drum rotation and various filtration zones allow for continuous filtration, cake drying, washing, and discharge.
3. Construction of Rotary Drum Filter
The main components of a rotary drum filter include:
Rotary Drum: The cylindrical drum is the primary rotating component, partially submerged in a slurry tank. The drum surface is perforated to allow liquid flow and is covered with filter media.
Filter Media: Filter cloth or mesh is stretched over the drum’s perforated surface, allowing liquid to pass while retaining solid particles.
Slurry Tank: This tank holds the slurry (solid-liquid mixture) in which the drum is partially submerged. The drum rotates through this slurry, capturing solids on its surface.
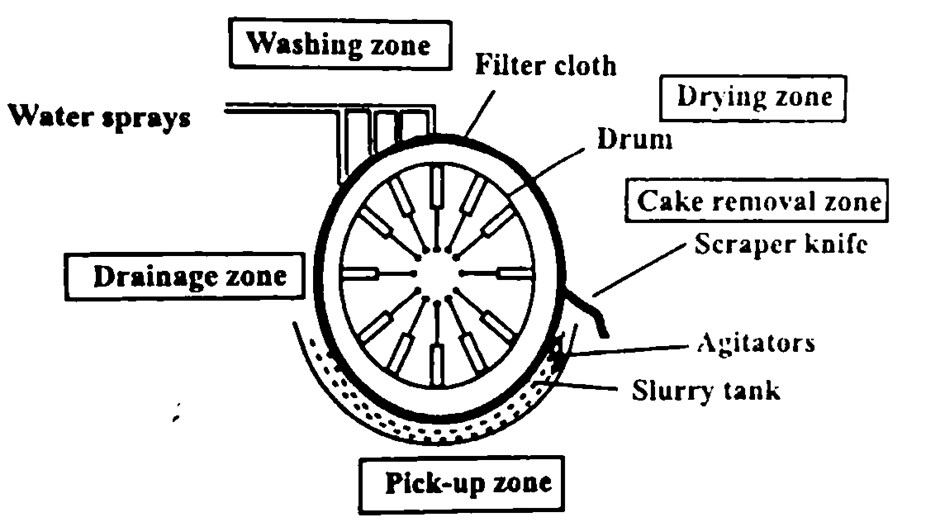
Vacuum System: A vacuum is applied to the inner section of the drum, creating a pressure differential that pulls liquid through the filter media.
Filtrate Receiver and Pump: A receiver collects the filtrate (liquid) that has passed through the drum, which is then pumped out for further processing or disposal.
Discharge System: This mechanism removes the filter cake from the drum surface. It may include scrapers, backflushing, or compressed air blowers to dislodge the cake.
Drive Mechanism: Motors and gears rotate the drum at a constant speed for continuous filtration.
4. Working of Rotary Drum Filter
The operation of a rotary drum filter involves multiple stages as the drum rotates through the slurry tank:
1. Filtration Stage: As the drum rotates through the slurry, vacuum pressure pulls the liquid through the filter media. The solid particles are retained, forming a filter cake on the drum’s surface.
2. Cake Drying: The cake moves out of the slurry and is exposed to the vacuum, which helps remove excess moisture and dry the cake.
3. Cake Washing (Optional): In some applications, a washing station sprays water or solvent onto the cake to remove impurities or wash out remaining filtrate.
4. Cake Discharge: As the drum rotates further, a scraper or backflush system removes the cake from the filter media surface.
5. Filtrate Collection: The filtrate is collected from the drum interior by the vacuum system and directed to a receiver, where it is pumped out for further use or disposal.
5. Uses of Rotary Drum Filter
Rotary drum filters are versatile and widely used in various industries:
Pharmaceutical Industry: For separating solids from fermentation broths and extracting active pharmaceutical ingredients (APIs) from suspensions.
Chemical Industry: Used for filtering out solid impurities from chemical solutions and separating intermediates.
Food and Beverage Industry: Commonly used for juice and wine clarification, sugar syrup filtration, and edible oil refining.
Mining and Metallurgy: Effective for dewatering mineral slurries, such as those in ore processing.
Wastewater Treatment: Removes suspended solids and dewaters sludge for more efficient disposal.
6. Merits of Rotary Drum Filter
The rotary drum filter offers numerous advantages:
Continuous Filtration: Allows for continuous processing, making it suitable for large-volume operations.
High Filtration Efficiency: Capable of handling high solid concentrations and offers efficient separation.
Multi-Stage Filtration: Performs filtration, washing, drying, and discharge in a single unit, streamlining the filtration process.
Wide Range of Applications: Versatile enough for a variety of industries and adaptable to different types of slurries.
Efficient Cake Washing: Enables effective washing of the filter cake, allowing high purity in some applications.
7. Demerits of Rotary Drum Filter
Despite its benefits, the rotary drum filter has limitations:
High Maintenance: The vacuum system, filter media, and discharge mechanism require regular maintenance to ensure continuous operation.
High Energy Consumption: The vacuum system and motorized drum rotation consume significant power, increasing operational costs.
Large Footprint: The setup requires substantial floor space, which may be a limitation in smaller facilities.
Clogging of Filter Cloth: Fine particles or viscous liquids can clog the filter media, reducing efficiency and necessitating frequent cleaning.
Lower Filtration Quality for Fine Particles: May not be ideal for applications requiring ultrafine filtration, as fine particles can clog the media and reduce the overall efficiency.
Conclusion
The rotary drum filter is a powerful, continuous filtration system widely employed in industrial settings for its efficiency and adaptability to high-throughput processes. While it requires careful maintenance and can have high operating costs, its ability to handle large slurry volumes and perform multiple functions makes it invaluable for industries such as pharmaceuticals, food processing, and wastewater management. Understanding the operating principles, design, and limitations of this filter helps optimize its performance in various applications.