Definition
A Silverson emulsifier is a high-shear mixing device specifically designed for emulsifying, homogenizing, and mixing a variety of liquid formulations, including those containing solids and powders. Known for its ability to create stable emulsions, it utilizes a unique rotor-stator design to generate high shear forces, which are essential for effective mixing in pharmaceutical applications.
Principles of Mixing with Silverson Emulsifiers
1. High Shear Mixing: The Silverson emulsifier operates on the principle of high shear mixing, where a rapidly rotating rotor draws materials into a mixing chamber. This rotor creates intense turbulence and shear, breaking down particles and ensuring thorough mixing.
2. Cavitation: As the rotor spins, it generates cavitation bubbles in the liquid. These bubbles collapse, producing localized high temperatures and pressures, which enhances the emulsification process and promotes the mixing of immiscible liquids.
3. Fluid Mechanics: The design promotes both axial and radial flow, which ensures a homogeneous mixture by allowing continuous circulation of materials through the mixing zone.
4. Mass Transfer: The high shear rates improve mass transfer between different phases, facilitating the formation of stable emulsions and dispersions.
Construction
1. Rotor and Stator: The core components of the Silverson emulsifier are the rotor and stator assembly. The rotor, mounted on a shaft, spins at high speeds, while the stator, which surrounds the rotor, has a series of slots or holes. This design increases the shear and dispersion of materials.
2. Motor: A powerful motor drives the rotor, with options for variable speed control to adjust the shear rates based on the formulation and mixing requirements.
3. Inlet and Outlet: The emulsifier typically features an inlet for introducing ingredients and an outlet for discharging the mixed product.
4. Mounting Frame: A robust frame supports the emulsifier assembly, ensuring stability during operation.
5. Vessel: The mixing vessel is designed to accommodate the emulsifier and can have features like baffles to enhance mixing efficiency.
Working
1. Installation: The Silverson emulsifier is positioned within a mixing vessel filled with the material to be emulsified or mixed.
2. Powering the Motor: The motor is activated, causing the rotor to spin rapidly.
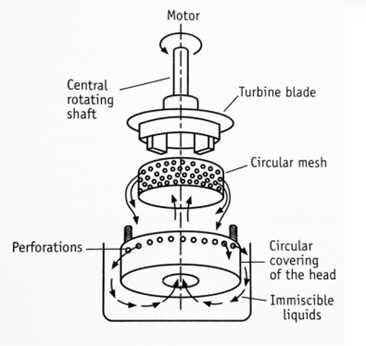
3. Fluid Motion: As the rotor spins, it draws the material into the mixing chamber. The high shear generated by the rotor-stator interaction breaks down particles and promotes emulsification.
4. Cavitation: The collapse of cavitation bubbles further enhances mixing, contributing to the formation of stable emulsions.
5. Monitoring and Control: Mixing parameters such as speed, duration, and temperature are monitored and can be adjusted for optimal emulsification conditions.
Uses
1. Emulsification: Silverson emulsifiers are widely used to create stable emulsions for creams, lotions, and other pharmaceutical formulations that require mixing immiscible liquids.
2. Homogenization: Ensures uniform distribution of active pharmaceutical ingredients (APIs) in liquid formulations.
3. Dispersing Solids: Effective in dispersing solid particles into liquids, which is useful for suspensions and ointments.
4. Dissolution: Facilitates the dissolution of powders in liquids, aiding in the preparation of solutions.
5. Mixing High Viscosity Products: Suitable for emulsifying and mixing products with high viscosity, such as gels, creams, and ointments.
Merits
1. High Efficiency: Provides rapid and effective mixing, significantly reducing processing times compared to traditional mixers.
2. Versatility: Capable of handling a wide range of formulations, including viscous and high-density materials.
3. Stable Emulsions: Produces emulsions that remain stable over time, essential for pharmaceutical products where separation is undesirable.
4. Scalability: Available in various sizes, making them suitable for both laboratory and large-scale production.
5. Adjustable Parameters: Offers variable speed and shear settings, allowing for customization based on specific mixing requirements.
Demerits
1. Initial Cost: The purchase cost of Silverson emulsifiers can be higher than that of traditional mixers due to their advanced design and technology.
2. Energy Consumption: High power requirements, particularly for larger units, can lead to increased operational costs.
3. Maintenance: The complex design may require more frequent maintenance and servicing compared to simpler mixing devices.
4. Not Suitable for All Applications: While effective for emulsifying, they may not be the best choice for applications that require gentle mixing or low shear.
5. Heat Generation: High shear mixing can generate heat, which may be detrimental to heat-sensitive formulations unless properly managed.
Conclusion
The Silverson emulsifier is a critical tool in the pharmaceutical industry for effective mixing, emulsification, and homogenization of a variety of liquid formulations. Its unique design and operational principles make it suitable for producing stable emulsions and ensuring uniformity in pharmaceutical products. Understanding the construction, working, uses, merits, and demerits of Silverson emulsifiers is essential for optimizing mixing processes in pharmaceutical manufacturing.