Definition
A turbine mixer is a type of mechanical mixing device commonly used in the pharmaceutical industry for the mixing of liquids and slurries. Turbines consist of a set of blades mounted on a rotating hub, designed to create a specific flow pattern within a liquid. They are crucial for achieving homogenous mixtures in various pharmaceutical processes.
Principles of Mixing with Turbines
1. Fluid Dynamics: Turbine mixers operate based on the principles of fluid dynamics, particularly utilizing the concept of shear force to induce mixing. The blades’ design promotes turbulent flow, which enhances mixing efficiency.
2. Shear and Energy Transfer: As the turbine blades rotate, they generate shear forces that break apart agglomerates and promote the dispersion of solids and gases within the liquid. The energy imparted to the fluid increases its kinetic energy, leading to enhanced mixing.
3. Flow Patterns: Turbines create specific flow patterns (axial or radial) depending on their design. Axial flow turbines direct the flow parallel to the axis of rotation, while radial flow turbines direct the flow perpendicular to the axis, affecting the mixing characteristics.
4. Residence Time: The mixing efficiency is also influenced by the residence time of the fluid in the mixing vessel, which can be optimized by adjusting the turbine speed and blade design.
Construction
1. Blades: The turbine blades are the most critical component, designed to maximize shear and turbulence. They can be flat, pitched, or curved and are typically made from stainless steel or other corrosion-resistant materials.
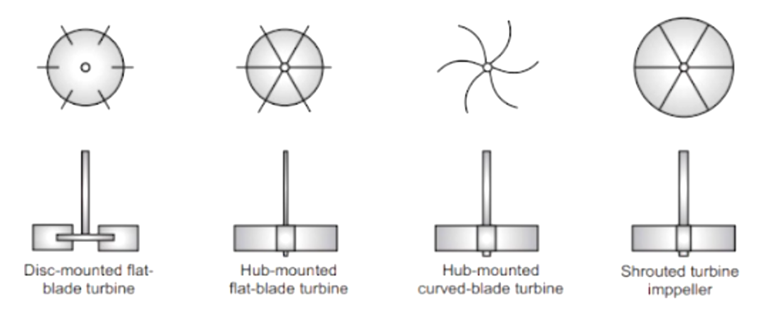
2. Hub: The central hub connects the blades to the shaft and provides structural integrity. It may also facilitate the attachment of the turbine to the motor.
3. Shaft: A robust shaft transmits the rotational force from the motor to the turbine blades.
4. Motor: The motor powers the turbine, and variable-speed options are often available to adjust mixing speeds based on process requirements.
5. Mounting Frame: The frame supports the entire assembly, ensuring stability during operation.
6. Vessel: The mixing vessel is designed to accommodate the turbine and can vary in size and shape depending on the application. Features like baffles may be included to enhance mixing efficiency.
Working
1. Installation: The turbine mixer is mounted within the mixing vessel, with blades submerged to an appropriate depth to facilitate mixing without causing excessive splashing.
2. Powering the Motor: The motor is activated, causing the shaft to rotate, which in turn spins the turbine blades.
3. Fluid Motion: As the blades rotate, they create zones of low and high pressure in the liquid, inducing flow. The turbulent flow pattern generated leads to the mixing of different phases (liquid, gas, solid) and enhances mass transfer.
4. Monitoring and Control: Parameters such as speed, mixing duration, and temperature are monitored and controlled to ensure optimal mixing conditions. Adjustments can be made in real time to achieve desired outcomes.
Uses
1. Homogenization: Turbine mixers are extensively used for homogenizing emulsions and suspensions, ensuring uniform distribution of active pharmaceutical ingredients (APIs).
2. Dissolution: They aid in dissolving solid substances into liquids, which is essential for creating solutions in pharmaceutical formulations.
3. Blending: Turbines effectively blend powders or granules with liquids, achieving a consistent mixture necessary for tablets and capsules.
4. Emulsification: Turbine mixers are capable of forming stable emulsions by combining immiscible liquids, such as oils and water, crucial in topical formulations and creams.
5. Heat Transfer: They facilitate heat transfer during processes such as sterilization or mixing of temperature-sensitive formulations.
Merits
1. High Efficiency: Turbine mixers provide rapid and effective mixing, which can significantly reduce processing times.
2. Versatility: They can be used for various liquid formulations, including those with high viscosity, making them suitable for a wide range of applications.
3. Scalability: Turbine mixers can be designed for both small-scale laboratory use and large-scale production, providing flexibility in pharmaceutical manufacturing.
4. Cost-Effectiveness: Once installed, turbine mixers have low operational costs, particularly in continuous mixing processes.
5. Customization: Turbines can be tailored to meet specific mixing requirements by modifying blade design, size, and motor speed.
Demerits
1. Energy Consumption: High power requirements, particularly for larger vessels or high viscosity fluids, can lead to increased operational costs.
2. Wear and Tear: Continuous operation can lead to wear on the blades, necessitating regular maintenance and replacement.
3. Heat Generation: Excessive mixing can generate heat, which may adversely affect heat-sensitive formulations.
4. Limited Mixing of Very Viscous Fluids: Turbine mixers may not be suitable for extremely viscous fluids, where other mixing methods (e.g., planetary mixers) may be more effective.
5. Potential for Aeration: Turbines may introduce air into the mixture, which can be detrimental to certain formulations, especially those sensitive to oxygen.
Conclusion
Turbine mixers are essential in the pharmaceutical industry for efficient mixing of various liquid formulations. Their design and operation can be optimized for specific applications, balancing the benefits of rapid mixing with potential drawbacks. Proper selection and use of turbine mixers can enhance the quality and consistency of pharmaceutical products, contributing to effective manufacturing processes.